ScioTeq’s secret optical bonding recipe
At ScioTeq we’ve been working hard to deliver our corporate vision for more than 35 years. We strongly believe in our promise to be ‘Your trusted partner for advanced visualization systems in the most extreme environments’. Ready for some unique insights in our display manufacturing activities? Let’s share the ScioTeq recipe with you.
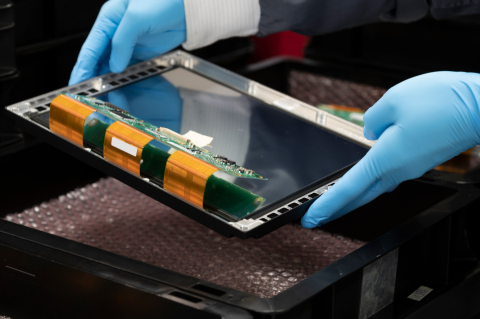
Far more than just an avionics, military or radar display
“From radar displays for Area Control Centers and military displays for Ground Combat Vehicles to large scale aircraft display models, our displays have to work perfectly every time. Be that in the desert, miles below the surface of the sea or on a landing strip in Siberia”, says Joost Iserbyt, Vice President of Operations at ScioTeq.
“The quality of our LCD displays is one of the reasons why operators feel they can trust our equipment implicitly. Tower display, industrial monitors or cockpit display. All ScioTeq displays feature an LCD panel layered with multiple filters, which improve the viewing angle, facilitate LCD panel temperature regulation and much more. And one of their greatest strengths is the technique used to fix them in place: optical bonding.”
Custom display manufacturer based in Belgium
The whole process of assembling ScioTeq displays – including optical bonding – is based at ScioTeq’s Kortrijk headquarters, home to one of the biggest cleanrooms in the Defense and Aviation industry worldwide for ruggedized display production. Here, we work in a perfectly controlled environment on the most challenging visualization solutions, from aircraft displays to military displays and much more. So, what’s our secret recipe? Let’s take a look in our kitchen…
Enjoy our optical quality checks and excellent lamination methods
Whether we assemble a primary flight display, or a frame grabber designed to use in a radar display, first step is always a thorough optical check of all components. This covers everything from dimensions to electrical connections and much more. It’s time-consuming, but it’s key to achieving optimal results.
Depending on the equipment, the ScioTeq experts opt for one of two lamination methods. Dry lamination ¬– in which the filters are bonded together with adhesive strips – is used for most avionics displays. Wet lamination, on the other hand, uses a liquid bonding agent, such as silicone. In both processes, the right mix of components is essential, as is a dust-free environment – and no air bubbles.
“And that just happens to be a field in which ScioTeq excels. Over the past 35 years, we have gradually perfected our lamination results, drawing on our experience producing avionics, military and radar displays that operate in the most extreme environments. You just cannot find this knowhow – or display quality – anywhere else. That’s why ScioTeq displays are one of the industry’s best-kept secrets. Only a few people know our final lamination recipe. I suspect that more people know the recipe for Coca Cola,” says Joost Iserbyt.
And the final secret ingredient is…
The finished LCDs, which can comprise up to eight layers, are integrated into the equipment based on another secret recipe. Only after hardening and stringent testing are the LED backlights fitted and the avionics, military and radar displays permitted to leave the cleanroom for final assembly. And yes, with around 14,000 laminations per year, our secret recipe is tried and true.
Do you like the taste of our recipe? Do you want more details and find out how we can help you achieve optimal situational awareness for your mission-critical applications? Contact us